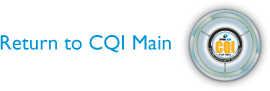
For additional information, please hover over the puzzle pieces to see a brief description
of each section. Click the puzzle piece once to freeze that information.
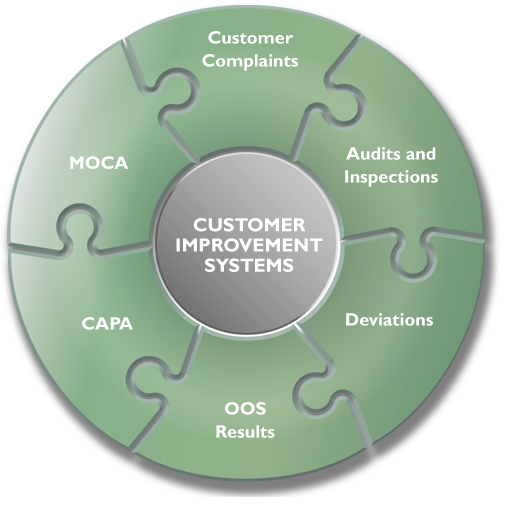
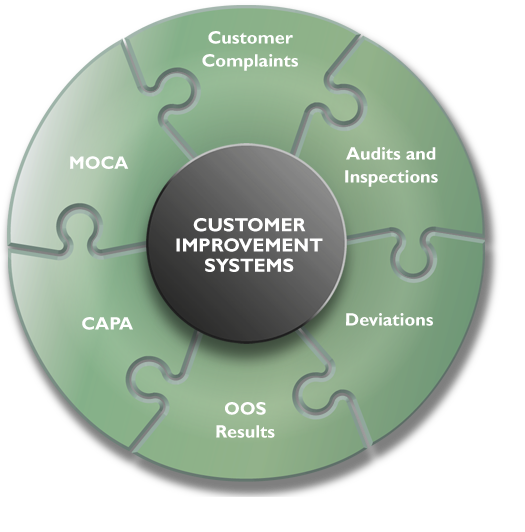
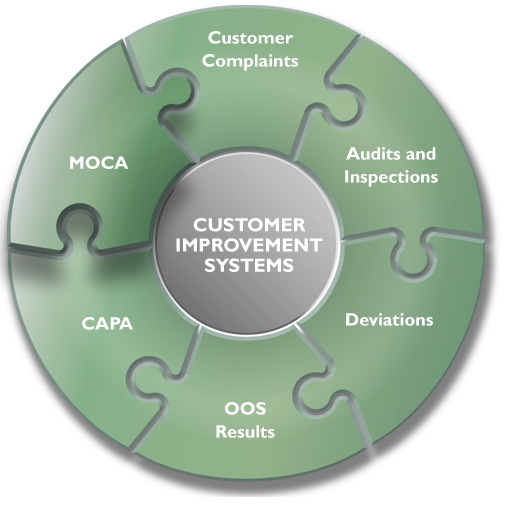
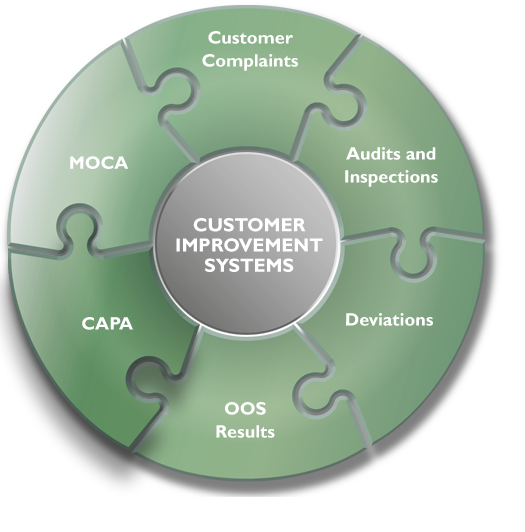
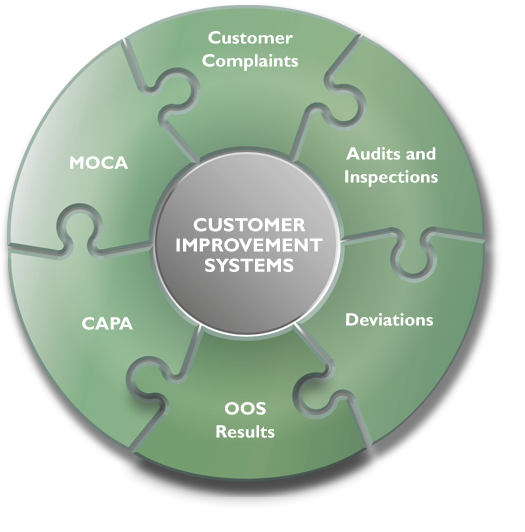
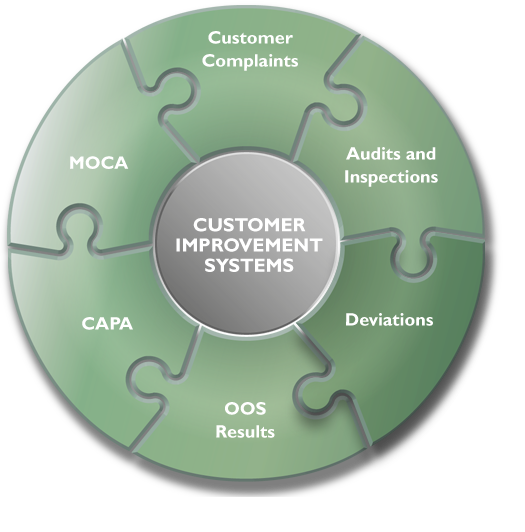
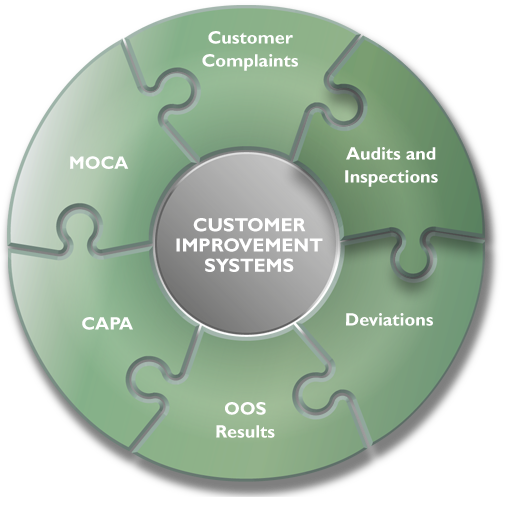
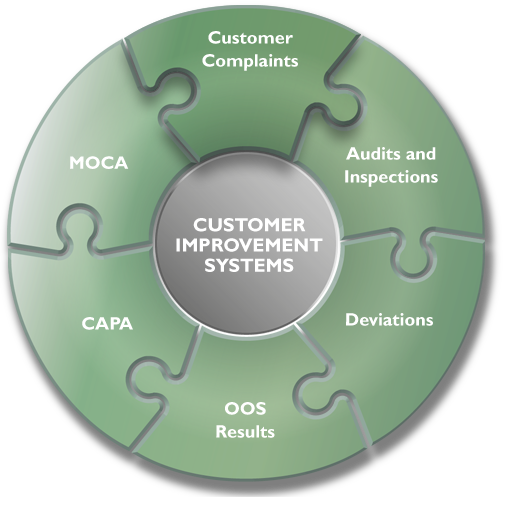
Customer Improvement Systems
Each of these systems is a source of valuable data that can be used to pinpoint critical areas for improvement, that can then be fed back into the system in a cycle of continuous improvement, resulting in higher quality, greater efficiency and lower costs. Each turn-key system is comprised of the necessary SOP’s, forms and tracking mechanisms that will serve as a starting point for the client.
For additional information on each system, please hoover over or click on a puzzle piece.
Customer Improvement Systems
Each of these systems is a source of valuable data that can be used to pinpoint critical areas for improvement, that can then be fed back into the system in a cycle of continuous improvement, resulting in higher quality, greater efficiency and lower costs. Each turn-key system is comprised of the necessary SOP’s, forms and tracking mechanisms that will serve as a starting point for the client.
For additional information on each system, please hoover over or click on a puzzle piece.
Management of Change Authorization (MOCA):
Not every new procedure or change to an existing procedure results in an improvement. Therefore, the implementation of new procedures or changes to existing procedures emanating from the CAPA system must be managed, and then monitored to determine effectiveness.
Corrective and Preventative Actions (CAPA):
Whether the issue is a customer complaint, audit/inspection observation, deviation or OOS result, the goal of the ensuing investigation is to identify the root cause and implement corrective and/or preventative actions to eliminate or minimize the probability of the issue reoccurring. Capturing and trending CAPA’s is an important source of information to determining if your improvement system is effective.
Out of Specification (OOS) Results:
Monitoring products and production systems with a comprehensive testing and inspection program sometimes results in an OOS result. Capturing, investigating and trending OOS results and implementing corrective and/or preventive actions, is a critical to minimizing the probability of future OOS results.
Deviations:
A good system for managing deviations from internal procedures is critical for tracking corrections to procedures that could not be followed due to internal or external circumstances. Capturing, investigating and trending deviations is an import source of information for identifying opportunities for improvement.
Audits and Inspections:
Client audits and regulatory agency inspections are a valuable source of information for identifying quality and regulatory issues with your quality systems. Capturing, investigating and trending both internal and external observations is critical to addressing both quality and regulatory issues.
Customer Complaints:
The number and type of customer complaints is an indication of the inherent quality of the products and services supplied to your client. Capturing, investigating and trending complaints is critical to identifying hidden quality and service issues.
» CQI Customer Improvement Systems
Customer Improvement Systems
Each of these systems is a source of valuable data that can be used to pinpoint critical areas for improvement, that can then be fed back into the system in a cycle of continuous improvement, resulting in higher quality, greater efficiency and lower costs. Each turn-key system is comprised of the necessary SOP’s, forms and tracking mechanisms that will serve as a starting point for the client.
For additional information on each system, please hoover over or click on a puzzle piece.
» CENTER
Customer Improvement Systems
Each of these systems is a source of valuable data that can be used to pinpoint critical areas for improvement, that can then be fed back into the system in a cycle of continuous improvement, resulting in higher quality, greater efficiency and lower costs. Each turn-key system is comprised of the necessary SOP’s, forms and tracking mechanisms that will serve as a starting point for the client.
For additional information on each system, please hoover over or click on a puzzle piece.
» MoCA
Management of Change Authorization (MOCA):
Not every new procedure or change to an existing procedure results in an improvement. Therefore, the implementation of new procedures or changes to existing procedures emanating from the CAPA system must be managed, and then monitored to determine effectiveness.
» CAPA
Corrective and Preventative Actions (CAPA):
Whether the issue is a customer complaint, audit/inspection observation, deviation or OOS result, the goal of the ensuing investigation is to identify the root cause and implement corrective and/or preventative actions to eliminate or minimize the probability of the issue reoccurring. Capturing and trending CAPA’s is an important source of information to determining if your improvement system is effective.
» OOS Results
Out of Specification (OOS) Results:
Monitoring products and production systems with a comprehensive testing and inspection program sometimes results in an OOS result. Capturing, investigating and trending OOS results and implementing corrective and/or preventive actions, is a critical to minimizing the probability of future OOS results.
» Deviation
Deviations:
A good system for managing deviations from internal procedures is critical for tracking corrections to procedures that could not be followed due to internal or external circumstances. Capturing, investigating and trending deviations is an import source of information for identifying opportunities for improvement.
» Audits and Inspections
Audits and Inspections:
Client audits and regulatory agency inspections are a valuable source of information for identifying quality and regulatory issues with your quality systems. Capturing, investigating and trending both internal and external observations is critical to addressing both quality and regulatory issues.
» Customer Complaints
Customer Complaints:
The number and type of customer complaints is an indication of the inherent quality of the products and services supplied to your client. Capturing, investigating and trending complaints is critical to identifying hidden quality and service issues.
Quality Assurance through the benefits of CQI
Speak to one of our services specialists at 888.396.2522 or email sales@dynalabs.us